Underwater Camera Enclosure for Robot Perception
As part of the GRASP ScalAR Lab, I designed and fabricated a waterproof enclosure for an underwater camera to support testing of computer vision algorithms in submerged environments. The goal was to create a reliable, reusable housing that could protect a camera and associated electronics during underwater experiments while ensuring clear, undistorted image capture. The enclosure enabled controlled testing of underwater perception techniques such as color correction, feature tracking, and object detection, contributing to a broader effort in underwater robotics and sensing.
The enclosure was designed for 35ft (~10m) depth and was successfully tested in shallow water conditions and integrated with vision pipelines for experimental validation
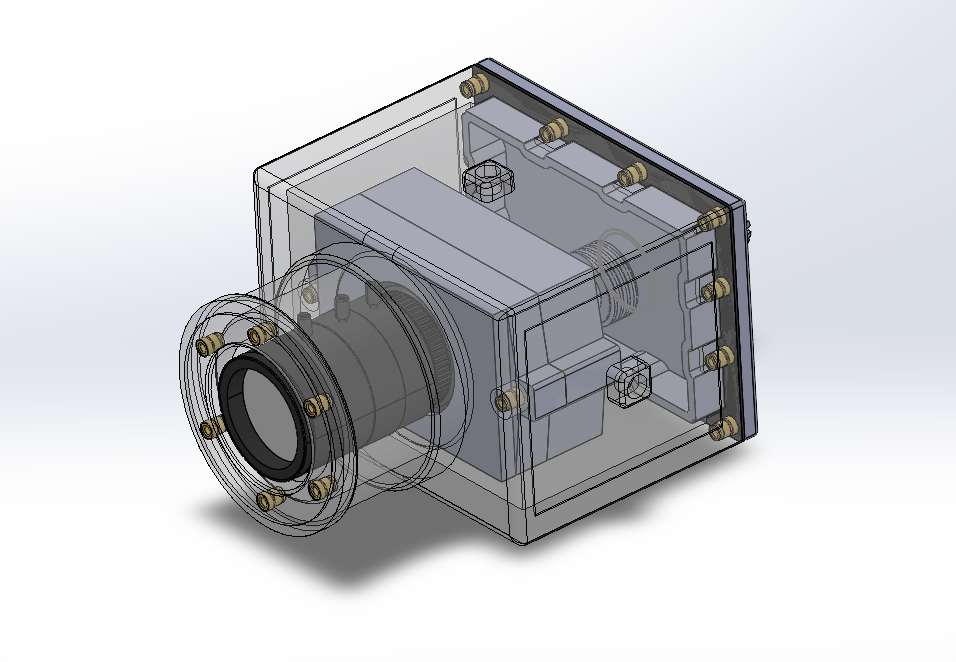
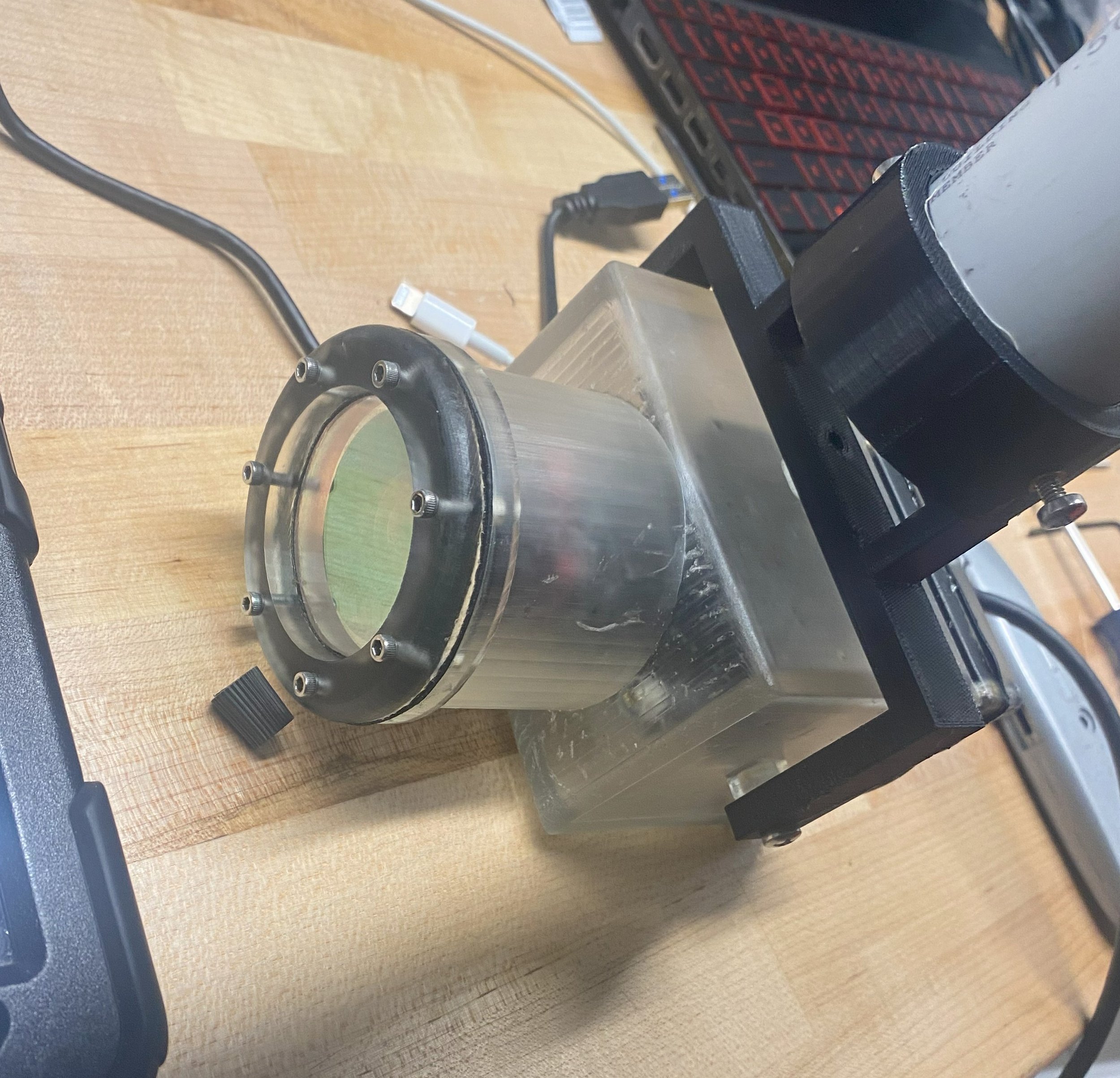
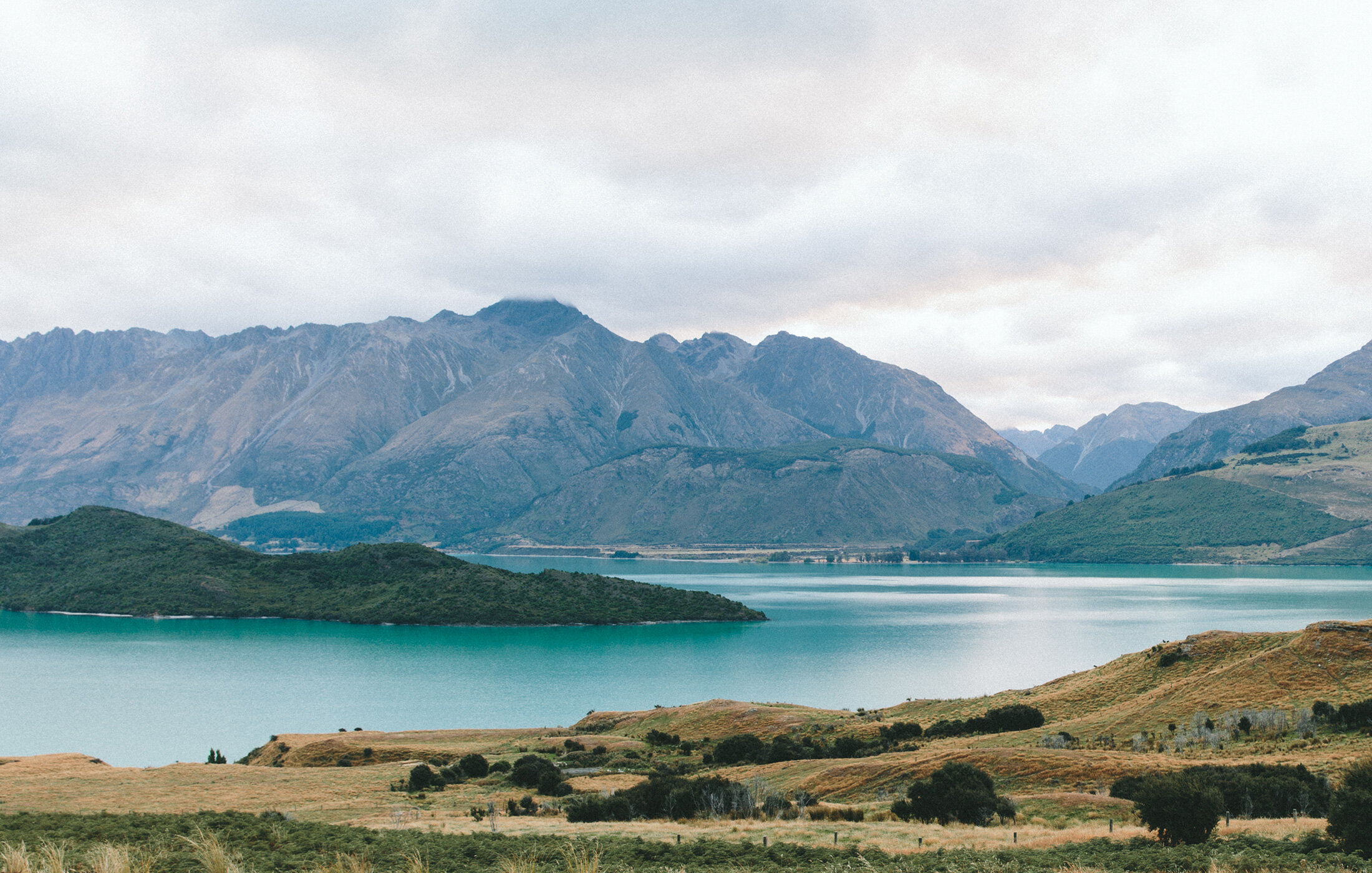

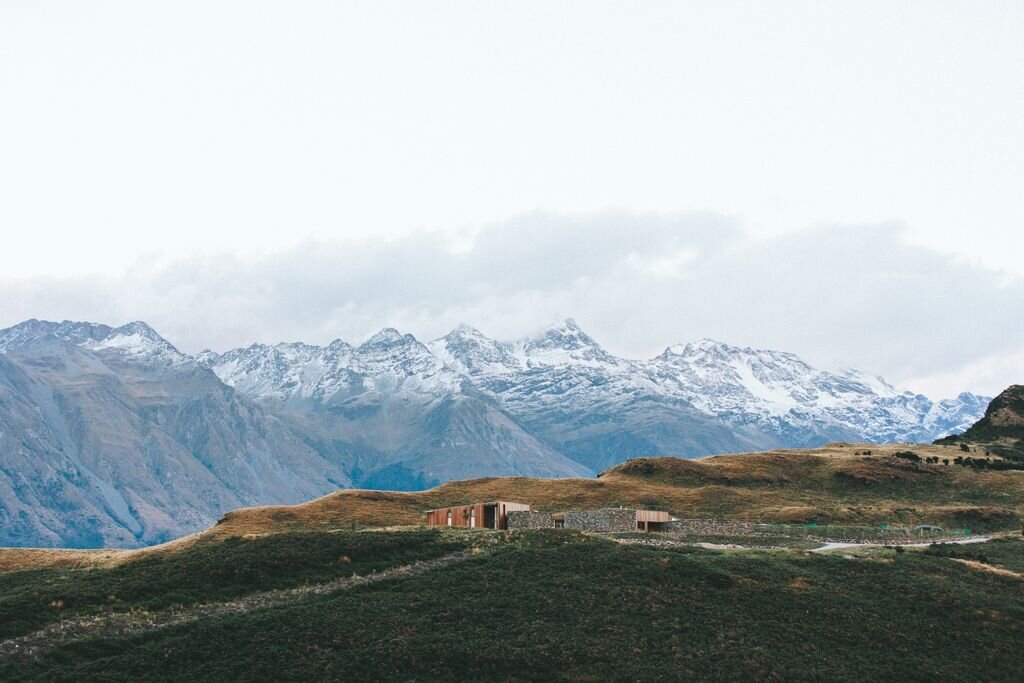
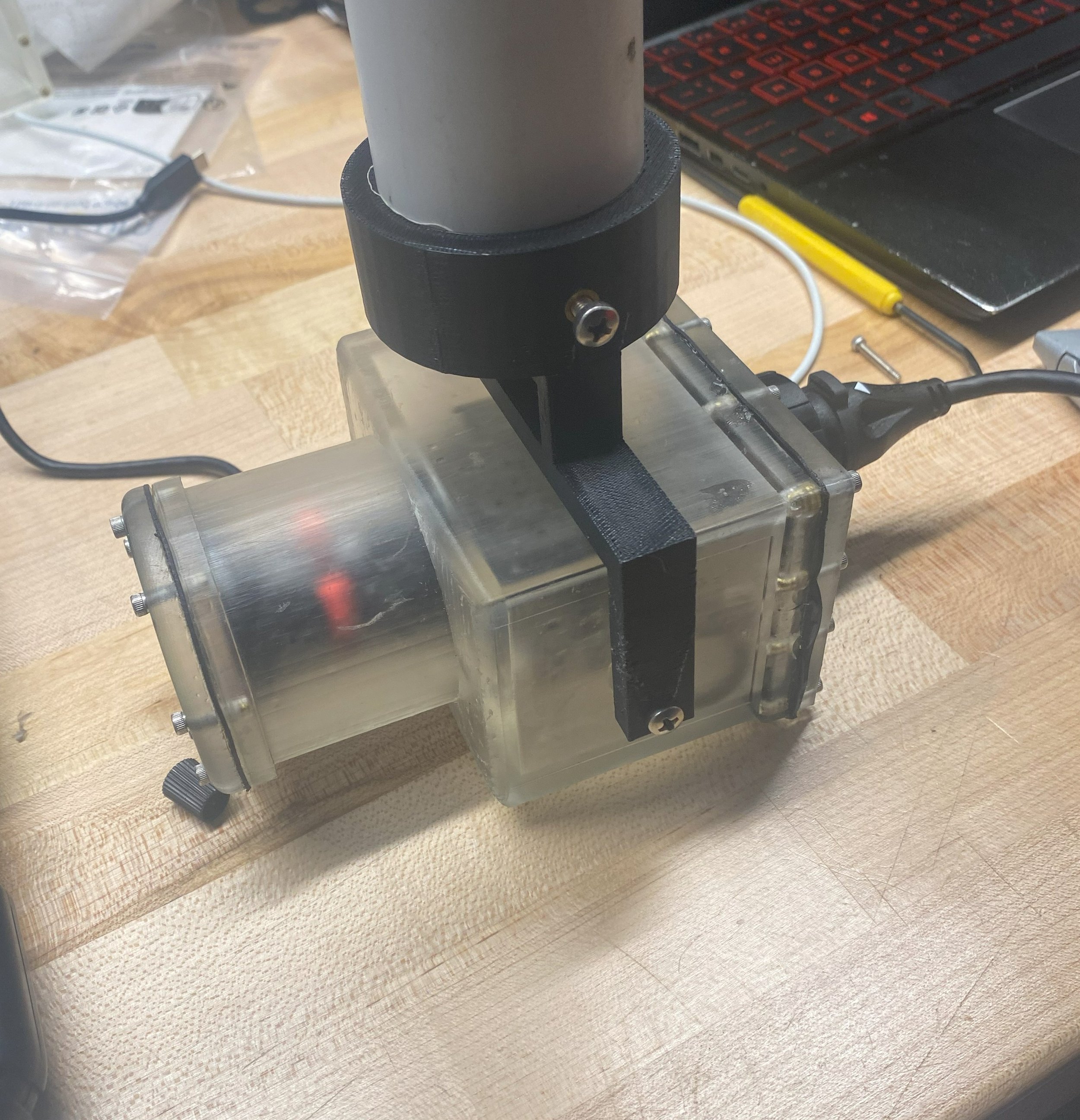
Project Work Breakdown
1. Design Objectives
Protect Experimental camera modules and electronics from water ingress.
Maintain high optical clarity and minimize image distortion.
Enable modular access for different camera modules, cable connections, and future sensor upgrades.
Ensure pressure resistance for required depth operation (~max. 10 meters).
Minimize bulk and maintain compact dimensions for integration on mobile underwater platforms.
2. Mechanical Design
CAD Modeling:
Designed in SolidWorks with precise tolerances for O-ring seals and fasteners.Materials Used:
Main Body: 3D-printed Resin.
Front Window: Optical glass
Gasket Seals: Neoprene gasket and EPDM O-rings to provide watertight sealing.
Fasteners: Stainless steel bolts with waterproof grease to resist corrosion.
Assembly Features:
Flanged sealing surface for window-to-body interface.
Internal mounting tray for Camera modules.
Rear cap with cable gland or watertight USB port.
3. Electrical Integration
Lighting (Modular Installation):
Waterproof LED strips integrated internally for illumination in murky or low-light environments.
Power and Data Access:
Penetrators or waterproof connectors routed through the back plate.
Cable gland to allow tethered USB or power cable without water ingress.
4. Testing and Validation
Leak Testing:
Submerged the enclosure in a Compression chamber under design FoS for 30+ minutes; checked for moisture inside.
Humidity Sensors utilized during tests on Enclosure
Tissue and silica gel packs used as indicators during initial dry runs.
Optical Testing:
Evaluated light refraction and field of view using underwater calibration targets.
Verified minimal image warping through the enclosure window.
Deployment:
Used in Lab Experiment tank to test underwater vision pipelines including feature detection, optical flow, and color correction.